Scotland’s Muirhead explains move into seat cover manufacturing
A significant force in aviation and transportation leather, Scotland’s Muirhead recently announced its expansion into seat cover manufacturing. The Seat Cover Service integrates every aspect of the production process — from initial design through testing, safety certification, and material production to seat cover manufacturing — and aims to remove complexity from the supply chain, enabling Muirhead... The post Scotland’s Muirhead explains move into seat cover manufacturing appeared first on Runway Girl.
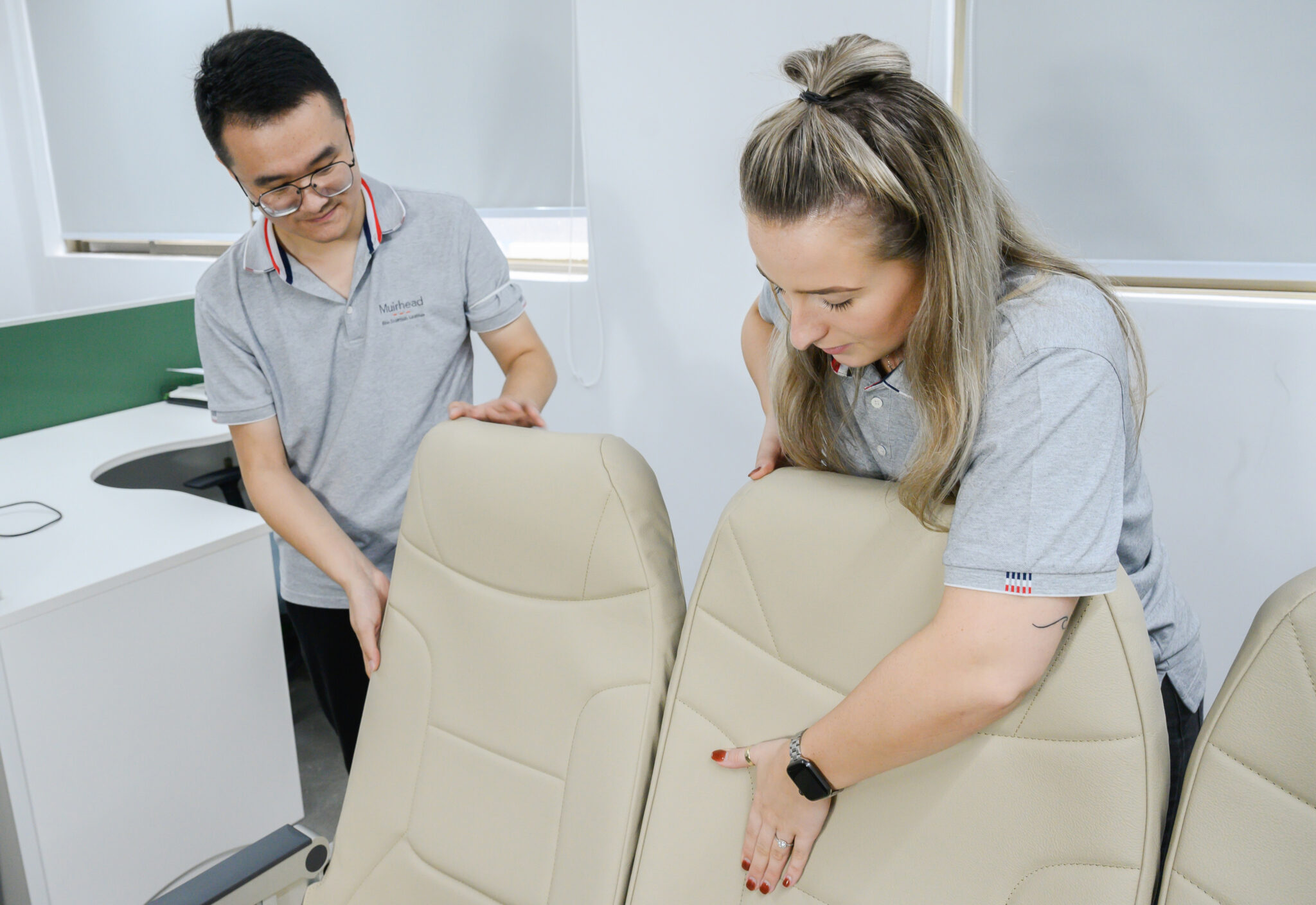
A significant force in aviation and transportation leather, Scotland’s Muirhead recently announced its expansion into seat cover manufacturing.
The Seat Cover Service integrates every aspect of the production process — from initial design through testing, safety certification, and material production to seat cover manufacturing — and aims to remove complexity from the supply chain, enabling Muirhead to deliver with reduced lead times, competitive pricing and guaranteed quality.
Muirhead combines its modern tanning plant and bleeding-edge production processes, built around strict sustainability goals, with over 180 years in the leather industry. But until now, it has not manufactured finished leather products.
So why take this step?
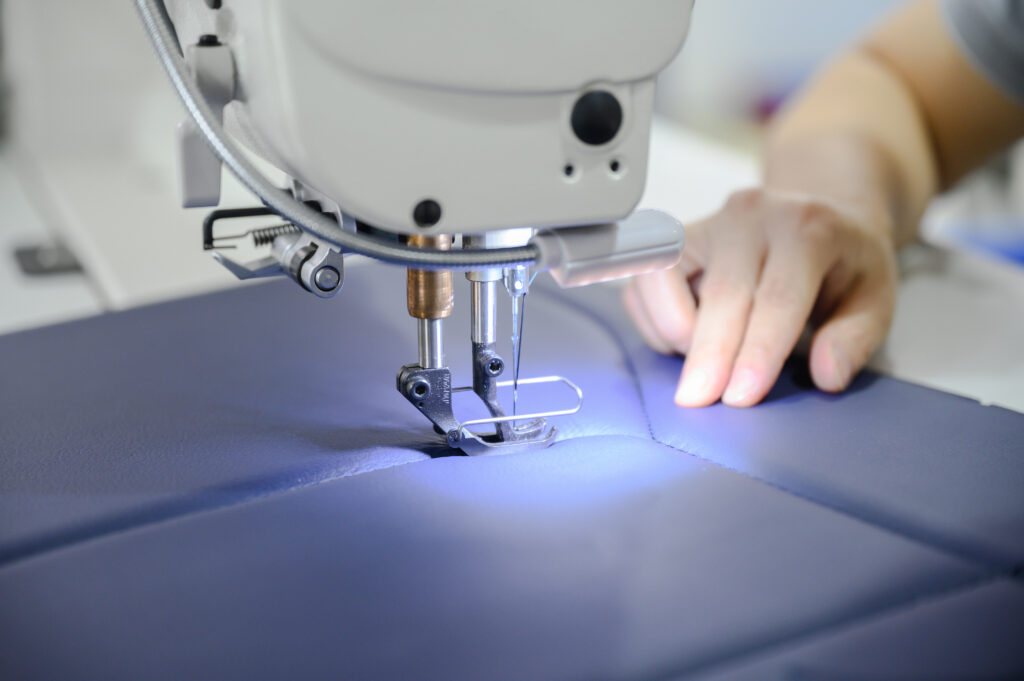
Muirhead has invested in the latest technology for its seat cover production facility. Image: Muirhead
Leather is a tough, resilient, natural product with inevitable variations in grain and other qualities between hides. These characteristics, which make it highly desirable as an aircraft seat cover material, also call for significant expertise and accuracy when patterns are made and leather is cut and sewn. ‘Cut and sew’ facilities familiar with fabrics and synthetics frequently fall foul of leather’s idiosyncrasies causing quality to suffer, according to Muirhead.
Setting up to cut and sew leather is therefore not something that happens overnight, even for the Scottish firm. Martin Longden, the company’s head of cabin engineering, agrees. “Around five years ago, the business decided it should expand its offer to include a service where customers could get completed seat covers from a single source.”
Rather than acquiring an existing leather cut and sew facility, Muirhead set out to create a genuine in-house capability. Longden himself brought along 20 years’ experience in the leather industry. He and fellow hire, pattern maker Scott Hadley, have already worked together for 15 years. More experts, including Charlotte Clayton, who runs the patterning department, subsequently came on board.
The cut and sew facility was established in Asia, in an area where automotive and apparel leather working expertise is abundant. The new factory employs the latest technology equipment, including CNC cutting and lamination machines, tooling and more.
Longden notes that Muirhead has no ambition to compete with companies working in fabrics and synthetics; its remit remains with leather. He highlights traditional points of friction within the supply chain, where leather has been processed poorly by manufacturers applying incorrect techniques, causing a drop-off in quality that can reverberate back and forth between airline customer, cover manufacturer, seat OEM and leather supplier.
“That’s not good for anyone, it doesn’t make for good relationships,” he continues. “Now, if there is a problem, the customer has only to come to us, but since we control the whole process, issues are less likely in the first place.”
Longden’s choice of the word ‘control’ barely does justice to Muirhead’s new Seat Cover Service. Considering the leather itself, the company takes in raw hides and performs the entire process, including tanning and dyeing, to produce hides ready to be used as a raw material for seat cover or other manufacturing.
Focusing on the seat cover, Longden says: “We really do offer a one-stop shop. We’ll go anywhere in the world and create patterns for retrofit covers on wing. The aircraft doesn’t need to come out of service because we’ll work during a night stop or hangar check. We then produce covers for a test fit, do the burn tests, EASA and other regulatory authority modifications, and help the airline install its first shipset of seat covers.”
Longden concludes: “It’s breaking news now, but we’ve actually been doing this for five years. We wanted to make sure everything was in place, that we could deliver the quality we wanted and run through a few projects. We already make up to 700 covers per month as spares for a European low-cost carrier and now we’re ready to step up into the mainstream.”
Related Articles:
- Soisa innovates with dress cover BFE program, sustainable armrest
- Muirhead promotes accessibility with neurodiverse-friendly seat covers
- Nature and sustainability inspire ReWILDing collection from Muirhead
- The role of anti-stain leather in Emirates’ impressive PE seats
- Sustainability proves key trend for inflight fabric: John Horsfall
- Tapping into real and “perceived” value with seat covers
- Scottish firm to breathe new life into old leather seat covers
Featured image credited to Muirhead
The post Scotland’s Muirhead explains move into seat cover manufacturing appeared first on Runway Girl.