Magazzino: 5 metodologie di classificazione delle scorte
Gli eventi disruptive degli ultimi anni hanno impattato sulle catene di fornitura, e hanno imposto alle aziende di ridefinire attori e nodi della filiera. Ritardi nella disponibilità di materiali, interruzioni e rallentamenti dei flussi logistici, aumento dei costi di trasporto hanno contribuito a trasformare la catena di distribuzione nelle aziende in tutto il mondo. Il magazzino ha assunto un ruolo sempre più centrale per una Supply chain efficace: è il fulcro da cui garantire il miglior servizio al cliente, la velocità di evasione degli ordini e il controllo dei costi. Una gestione efficiente, però, parte da una corretta classificazione delle scorte. Esistono diversi approcci alla classificazione delle scorte e ogni realtà aziendale, a seconda del suo settore di riferimento, delle sue logiche distributive e del suo modello di business, deve individuare la metodologia più adatta al proprio caso, al fine di ridurre i costi operativi e massimizzare la disponibilità delle merci. Ecco cinque metodologie di classificazione delle scorte. 1 - Metodo ABC Il Metodo ABC è una tecnica di classificazione utilizzata per ottimizzare la gestione delle scorte in base al loro valore e alla loro frequenza di utilizzo. Derivato dall'analisi di Pareto, si basa sul principio secondo cui una piccola percentuale di articoli rappresenta una parte significativa del valore totale delle scorte. Gli articoli sono suddivisi in tre categorie: Classe A: comprende articoli ad alto valore economico o con alta rotazione. Generalmente rappresentano il 20% degli articoli, ma costituiscono circa l'80% del valore totale del magazzino. Questi articoli richiedono monitoraggio continuo, politiche di riordino rigorose e previsioni accurate della domanda. Classe B: include articoli di valore medio, che rappresentano circa il 30% degli articoli e il 15% del valore totale. La gestione è intermedia, con controlli periodici e strategie di riordino bilanciate. Classe C: comprende articoli di basso valore o bassa rotazione, che costituiscono il 50% degli articoli, ma solo il 5% del valore totale. Per questi, si adottano metodi di gestione semplificati, con scorte più elevate per ridurre i costi amministrativi. L’adozione del Metodo ABC consente di concentrare le risorse di gestione sugli articoli più critici, migliorando l’efficienza operativa e riducendo i costi complessivi di gestione del magazzino. 2 - Classificazione per valore o per rotazione Un’altra metodologia di classificazione delle scorte è quella basata sul valore economico totale dei prodotti, o sulla velocità di rotazione degli articoli. Nella classificazione per valore, l'attenzione è focalizzata sul contributo complessivo che ciascun prodotto porta al fatturato aziendale. È possibile così individuare gli articoli col maggior ritorno economico, che necessitano quindi di maggiore controllo. La classificazione per rotazione, invece, si basa sulla velocità e sulla frequenza con cui le scorte vengono rinnovate. Ai prodotti con alta rotazione si dedica elevata priorità, per garantire sempre continuità operativa e soddisfazione del cliente. 3 - Metodo FIFO, First In, First Out L’approccio FIFO (First In, First Out) è quello più utilizzato in contesti dove la data di scadenza o la qualità del prodotto sono fattori critici, si pensi per esempio al settore alimentare o in generale a tutti quelli di prodotti con scadenza temporale. Il sistema prevede che le merci immagazzinate per prime siano anche le prime a essere utilizzate o spedite. Si basano sulla metodologia FIFO i settori come l’alimentare, il farmaceutico o il chimico, per minimizzare gli sprechi e garantire la conformità normativa. Dal punto di vista delle implicazioni pratiche, questo metodo richiede un’elevata capacità di organizzare gli spazi e di tracciare e catalogare le scorte in modo preciso. 4 - Metodo LIFO, Last In, First Out Esattamente contrapposto al FIFO, c’è il metodo LIFO (Last In, First Out): questo prevede che le ultime scorte immagazzinate siano le prime a essere utilizzate e a lasciare il magazzino. Questo approccio è utilizzato nei contesti di mercato in cui i costi di acquisto sono instabili, si alzano e abbassano frequentemente, e si ha quindi la necessità di contabilizzare prima le merci più costose. Questo approccio, tuttavia, non è adatto a quei settori merceologici in cui la qualità del prodotto tende a deteriorarsi nel tempo o i prodotti possono scadere. Dal punto di vista pratico, è importante pianificare in modo preciso la gestione delle scorte per evitare accumuli di stock obsoleti. 5 - Just in Time e Just in Case Il Just in Time (JIT) è un approccio che nasce con l’obiettivo di minimizzare le scorte a magazzino, approvvigionando le merci solo nel momento in cui sono necessarie, riducendo lo stock al minimo indispensabile. Questo metodo è vantaggioso per aziende che operano in settori caratterizzati da variabilità della domanda, com il manifatturiero. Riducendo i costi di stoccaggio, si m

Gli eventi disruptive degli ultimi anni hanno impattato sulle catene di fornitura, e hanno imposto alle aziende di ridefinire attori e nodi della filiera.
Ritardi nella disponibilità di materiali, interruzioni e rallentamenti dei flussi logistici, aumento dei costi di trasporto hanno contribuito a trasformare la catena di distribuzione nelle aziende in tutto il mondo. Il magazzino ha assunto un ruolo sempre più centrale per una Supply chain efficace: è il fulcro da cui garantire il miglior servizio al cliente, la velocità di evasione degli ordini e il controllo dei costi.
Una gestione efficiente, però, parte da una corretta classificazione delle scorte. Esistono diversi approcci alla classificazione delle scorte e ogni realtà aziendale, a seconda del suo settore di riferimento, delle sue logiche distributive e del suo modello di business, deve individuare la metodologia più adatta al proprio caso, al fine di ridurre i costi operativi e massimizzare la disponibilità delle merci.
Ecco cinque metodologie di classificazione delle scorte.
1 - Metodo ABC
Il Metodo ABC è una tecnica di classificazione utilizzata per ottimizzare la gestione delle scorte in base al loro valore e alla loro frequenza di utilizzo. Derivato dall'analisi di Pareto, si basa sul principio secondo cui una piccola percentuale di articoli rappresenta una parte significativa del valore totale delle scorte.
Gli articoli sono suddivisi in tre categorie:
Classe A: comprende articoli ad alto valore economico o con alta rotazione. Generalmente rappresentano il 20% degli articoli, ma costituiscono circa l'80% del valore totale del magazzino. Questi articoli richiedono monitoraggio continuo, politiche di riordino rigorose e previsioni accurate della domanda.
Classe B: include articoli di valore medio, che rappresentano circa il 30% degli articoli e il 15% del valore totale. La gestione è intermedia, con controlli periodici e strategie di riordino bilanciate.
Classe C: comprende articoli di basso valore o bassa rotazione, che costituiscono il 50% degli articoli, ma solo il 5% del valore totale. Per questi, si adottano metodi di gestione semplificati, con scorte più elevate per ridurre i costi amministrativi.
L’adozione del Metodo ABC consente di concentrare le risorse di gestione sugli articoli più critici, migliorando l’efficienza operativa e riducendo i costi complessivi di gestione del magazzino.
2 - Classificazione per valore o per rotazione
Un’altra metodologia di classificazione delle scorte è quella basata sul valore economico totale dei prodotti, o sulla velocità di rotazione degli articoli.
Nella classificazione per valore, l'attenzione è focalizzata sul contributo complessivo che ciascun prodotto porta al fatturato aziendale. È possibile così individuare gli articoli col maggior ritorno economico, che necessitano quindi di maggiore controllo.
La classificazione per rotazione, invece, si basa sulla velocità e sulla frequenza con cui le scorte vengono rinnovate. Ai prodotti con alta rotazione si dedica elevata priorità, per garantire sempre continuità operativa e soddisfazione del cliente.
3 - Metodo FIFO, First In, First Out
L’approccio FIFO (First In, First Out) è quello più utilizzato in contesti dove la data di scadenza o la qualità del prodotto sono fattori critici, si pensi per esempio al settore alimentare o in generale a tutti quelli di prodotti con scadenza temporale. Il sistema prevede che le merci immagazzinate per prime siano anche le prime a essere utilizzate o spedite.
Si basano sulla metodologia FIFO i settori come l’alimentare, il farmaceutico o il chimico, per minimizzare gli sprechi e garantire la conformità normativa. Dal punto di vista delle implicazioni pratiche, questo metodo richiede un’elevata capacità di organizzare gli spazi e di tracciare e catalogare le scorte in modo preciso.
4 - Metodo LIFO, Last In, First Out
Esattamente contrapposto al FIFO, c’è il metodo LIFO (Last In, First Out): questo prevede che le ultime scorte immagazzinate siano le prime a essere utilizzate e a lasciare il magazzino. Questo approccio è utilizzato nei contesti di mercato in cui i costi di acquisto sono instabili, si alzano e abbassano frequentemente, e si ha quindi la necessità di contabilizzare prima le merci più costose. Questo approccio, tuttavia, non è adatto a quei settori merceologici in cui la qualità del prodotto tende a deteriorarsi nel tempo o i prodotti possono scadere. Dal punto di vista pratico, è importante pianificare in modo preciso la gestione delle scorte per evitare accumuli di stock obsoleti.
5 - Just in Time e Just in Case
Il Just in Time (JIT) è un approccio che nasce con l’obiettivo di minimizzare le scorte a magazzino, approvvigionando le merci solo nel momento in cui sono necessarie, riducendo lo stock al minimo indispensabile. Questo metodo è vantaggioso per aziende che operano in settori caratterizzati da variabilità della domanda, com il manifatturiero. Riducendo i costi di stoccaggio, si migliora il flusso di cassa e si aumenta la flessibilità operativa. Tuttavia, dal punto di vista pratico questa metodologia necessita di una una supply chain integrata e affidabile, per evitare ritardi che potrebbero compromettere l’operatività. Per questo motivo, negli ultimi anni sempre più aziende sono passare dal Just in Time al Just in Case (JIC), cioè prevedendo di rifornire o stoccare prodotti in anticipo, per essere sicuri di avere scorte sufficienti in magazzino e garantire la continuità operativa anche nel caso di imprevisti o interruzioni nella Supply chain.
What's Your Reaction?
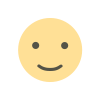
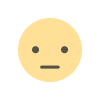
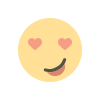
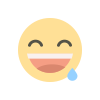
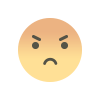
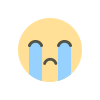
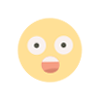